根据内防腐层管道的特性,内防腐层一般都需要涂敷两遍以上,监测每次涂敷的湿膜厚度可有效地预测防腐层的干膜厚度。这样,就可计算出徐敷的次数,提高生产效率,保证防腐层厚度。 当环境相对湿度大于85%时,处理后的钢管易返锈;钢管潮湿,影响涂料粘结力,也是影响产品质量的一项重要因素。因此,严禁在雨、雪、雾及风沙等气候条件下露天作业.涂塑钢管已经广泛应用于石油、化工、建筑、造船、通讯、电力和地下输气管道等众多领域。
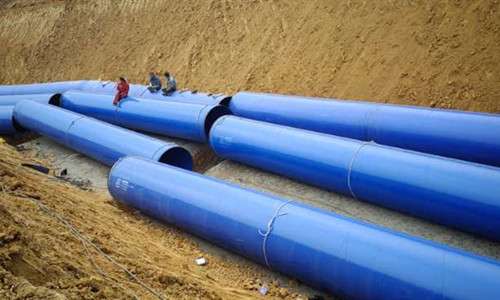
涂敷工艺 a)涂料配置 目前在各油田使用的液体环氧涂料都是双组份,甲组份为涂料,乙组份为固化剂。双组份涂料的优点是可以配制成高固体含量的废料,甲、乙组份分装,保存时间相对长一些,便于存放。使用时,涂料的配比相当重要,而每一种涂料的配比都不相同,因此,配料时,应根据产品说明书的要求比例和方法进行配制。 b)钢管内表面预处理是一项关键工作,没有一个清洁的表面就不可能有一个高质量的防腐层。因为不清洁的表面,等于在防腐层与钢管内表面之间有一层隔离层,大大影响了防腐层与钢管表面的粘结力。如粘结力不好,防腐层在管道运行过程中脱落,脱落的防后层夹带在输送介质中,将对介质和油田生产带来不良后果,甚至于堵塞油井及管件,致使生产中断;另外防腐层脱落后的钢管表面将会受到介质的腐蚀。采用喷(抛)丸除锈,其表面预处理的质量应达到《涂装前钢材表面锈蚀等级和除锈等级》中规定的 Sa2级要求。 c)喷(抛)射处理后,应用清洁、干燥、无油的压缩空气将钢管内部的可能存在一些砂粒、尘埃、锈粉等微尘清除干净。经喷(抛)射处理后的钢管应立即进行涂装,以防钢管内表面重新返锈或污染,而影响防腐层质量。如果钢管内表面已经返锈或被污染,那么必须重新进行表面预处理,以保证防腐层的质量。 d)钢管涂敷,由于涂料在使用前一般都放置了一定时间,涂料有沉淀现象,因此,在开桶前应晃动,使涂料混合均匀。 e)钢管内表面涂敷是一项非常重要的工序,涂敷的好坏直接关系到产品的使用性能。目前 液体环氧涂料的涂敷主要采用喷涂工艺。根据液体环氧涂料的性能,采用喷涂工艺施工.效果比较理想。生产前应先调整设备,设定工艺参数,喷涂可使液体环氧涂料充分雾化,喷出料均匀,在钢管内表面上形成厚度均匀的防腐层